Understanding UV Inkjet Technology
Terms to understand with UV Inkjet
- Surface Energy
- Wettability
- Photo-initiators
- Dyne level
- Adhesion (bonding)
- Curing
- Dwell Time
UV vs. Aqueous based Inkjets
The primary difference between UV and aqueous inkjet printing is how the ink converts from a liquid to a solid:
- UV inkjets convert UV ink from a liquid to a solid through a chemical reaction from UV energy
- Aqueous (water) inkjets use heat energy to evaporate water, leaving pigments and dye in the substate
Key points about UV inkjet:
- Curing mechanism:
- Uses ultraviolet light to rapidly cure the ink, turning it from liquid to solid almost instantly.
- Durability:
- Offers superior scratch and abrasion resistance due to the fast curing process.
- Glossy finish:
- Can produce a very high gloss appearance.
- Suitable substrates:
- Can print on a wide range of materials like plastic, metal, glass, and certain types of paper.
Key points about aqueous inkjet:
- Drying mechanism:
- Dries through water evaporation from the ink.
- Environmental impact:
- Considered more environmentally friendly as it uses water-based ink.
- Cost-effective:
- Generally a more affordable option compared to UV.
- Suitable substrates:
- Primarily used on paper and other absorbent materials
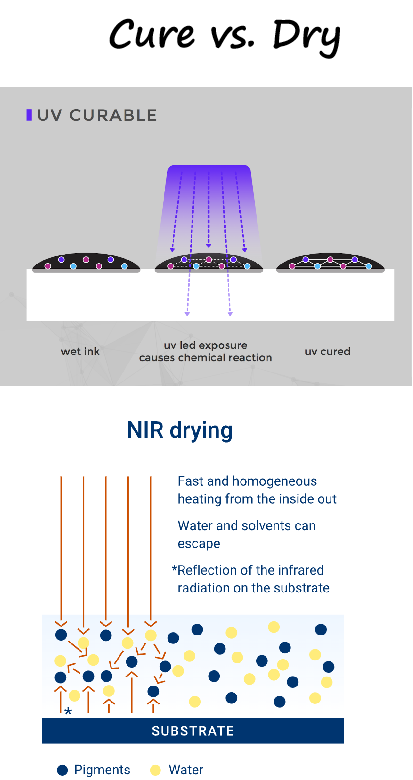
UV inkjet Drops based on dyne levels
Key points about UV inkjet printing:
The ink used in UV printers is formulated with photo-initiators that react to UV light, causing the ink to rapidly polymerize and solidify when exposed to it.
Immediately following the ink deposition, a UV lamp (often LED-based) emits ultraviolet light to cure the ink almost instantly.
Versatility
How the process works in detail:
- Ink droplet deposition:
- The print head precisely sprays tiny droplets of UV ink onto the substrate, forming the desired image.
- UV light exposure:
- As the ink is deposited, a UV lamp directly illuminates the area, triggering a chemical reaction in the ink, causing it to rapidly solidify and bond.
Benefits of UV inkjet printing:
- Fast drying time: The instant curing of the ink eliminates the need for a drying stage, allowing for quick turnaround times.
- High print quality: Precise ink placement and quick curing lead to sharp, detailed prints.
- Wide range of substrates: UV printing can be used on various materials like plastic, acrylic, metal, glass, and even wood.
- Durable prints: The cured UV ink is resistant to scratches and fading.
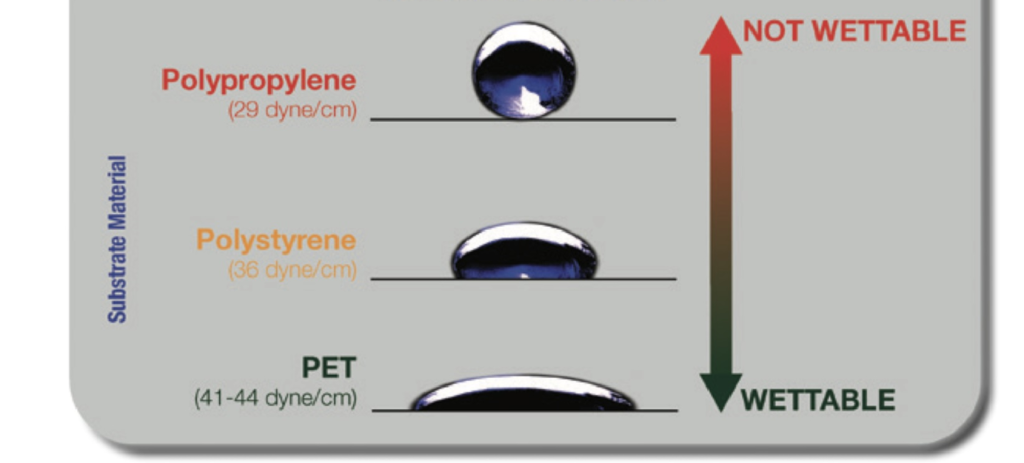
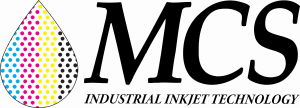
Dyne level
Dyne level is a measurement of a material’s surface energy, or how well liquids adhere to it. It’s measured in dynes per centimeter (\(dynes/cm\)) or millinewtons per meter (\(mN/m\)).
What it’s used for
- Adhesion: Dyne level is important for determining how well a coating, paint, or adhesive will stick to a surface.
- Wettability: Dyne level indicates how well a liquid will wet (spread) on a surface.
- Manufacturing: Dyne level is used to assess how a material will react to manufacturing processes like printing, painting, and coating.
How it’s measured:
A dyne test is used to measure a material’s dyne level. This test involves applying a liquid with a known dyne level to the material. If the liquid wets out the surface, the material has a higher dyne level. Dyne pens can be used to apply the liquid to the surface.
Factors that affect dyne level
- Temperature: The relationship between temperature and surface energy can vary between materials.
- Contamination: Dirty surfaces have lower wettability. Surface preparation: Low surface energy can indicate that a material needs surface treatment.
For optimal inkjet printing, a recommended dyne reading for a substrate is typically between 38 and 40 dynes/cm; with many experts considering 40 dynes/cm as the ideal level for most plastic substrates, ensuring good ink adhesion without causing excessive static issues.
Key points about dyne levels and inkjet printing:
- Lower dyne levels:
- If the dyne level is below 38, ink adhesion may be poor, requiring additional surface treatment on the substrate.
- Higher dyne levels:
- While a higher dyne level generally indicates better adhesion, exceeding 50 dynes/cm can lead to handling problems related to static electricity.
- Testing is crucial:
- Always test the dyne level of your specific substrate before printing to ensure compatibility with your chosen ink.
UV inkjet Adhesion (bonding)
UV inkjet Adhesion or bonding is the process of using UV-curable ink to stick to a substrate, or surface. UV ink is cured by exposure to UV light during printing, and it can bond to a wide range of materials.
Factors that affect UV inkjet bonding
- Surface preparation: The surface should be clean and free of dust, oil, and other dirt.
- Surface energy: The surface energy of the substrate should be slightly higher than the surface tension of the ink.
- Amount of ink: Using more ink can improve adhesion because it increases the contact area.
- Primer: A UV adhesion promoter, or primer, can help the ink bond to low surface energy substrates.
- Undercoat: Applying a clear undercoat, like a matte varnish, can improve adhesion on some substrates.
How to improve UV inkjet bonding
- Use a UV adhesion promoter, or primer, designed for the substrate
- Clean the surface thoroughly
- Apply a clear undercoat, like a matte varnish
- Use more ink
Techniques for ensuring Curing UV Inkjet
- Increase Dwell Time
- Slow down transport, increasing time under UV lamp
- Turn direction of UV lamp 90 degrees, increasing dwell time of UV energy
- Reduce the volume of ink
- Reduce DPI
- Reduce Drop size
UV Inkjet Glossary
What are photoinitiators?
Photoinitiators are small molecules in UV inkjet ink that absorb UV light and start a chemical reaction that converts ink form a liquid to a solid.
How they work
- Photoinitiators absorb UV light energy
- The energy is converted into chemical energy
- The chemical energy produces reactive species, such as free radicals
- The reactive species interact with the ink’s active components
- This interaction starts a chemical reaction called photopolymerization
- The result is a cross-linked polymer that converts to a solid quickly
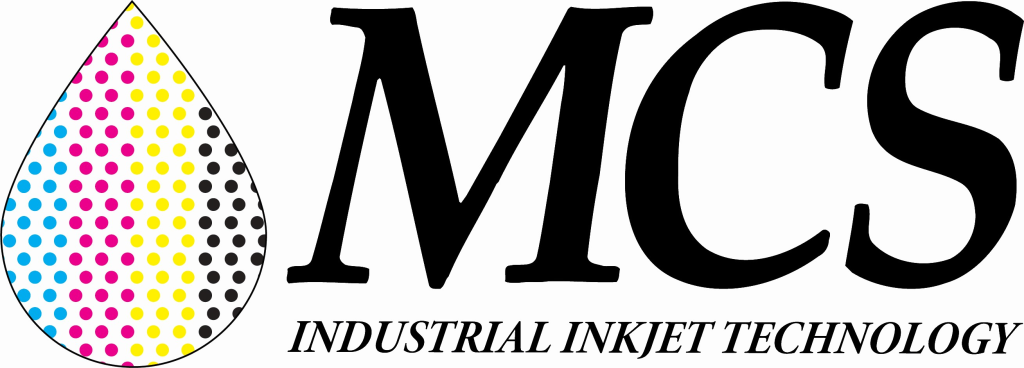
Common photoinitiators
Benzophenone, Acetophenone, Thioxanthone, Hydroxyketones, Iodonium salts, and Sulfonium salts.
Factors to consider
- The choice of photoinitiator can affect the curing speed and the final properties of the ink
- The right amount of photoinitiator is needed to achieve the desired results
- Tests should be performed to determine the right amount and speed
- UV inkjet curing is a printing process where a specially formulated ink is instantly cured by exposure to high-intensity ultraviolet (UV) light immediately after being printed by an inkjet printer, essentially fixing the ink onto the substrate in a very short time frame, resulting in a fast and precise print with minimal smudging; the “UV” refers to the ultraviolet light used for curing the ink.
Key points about UV inkjet curing:
- Fast curing:
- The primary benefit is the near-instantaneous curing of the ink, making it ideal for high-speed printing applications.
- Photochemical reaction:
- UV light triggers a chemical reaction within the ink, causing the molecules to cross-link and solidify.
- UV curable inks:
- Special inks are required that contain photoinitiators which react to UV light to initiate the curing process.
- Wide range of substrates:
- UV inkjet printing can be used on various materials like plastic, metal, glass, and paper.
- Environmentally friendly:
- UV inks often have low or no volatile organic compounds (VOCs).
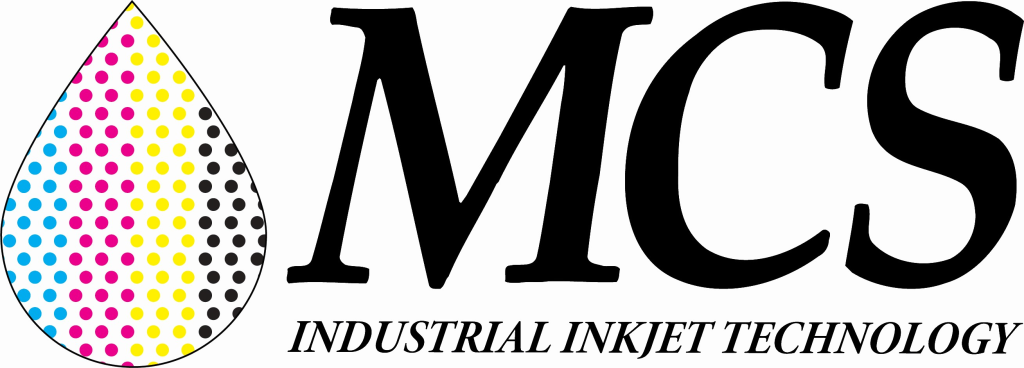
Dyne Levels
When discussing UV inkjet printing, “low dyne levels” refer to a substrate material with a surface energy that is too low for optimal adhesion of UV ink, typically meaning the material’s dyne level is below the range of 35-45 dynes, where most UV inks fall within a 25-35 dyne range; to achieve good adhesion, the substrate’s dyne level should be slightly higher than the ink’s dyne level, often requiring a primer or surface treatment to increase the surface energy.
Key points about low dyne levels in UV inkjet printing:
- Ink adhesion issues:
- If a substrate has a low dyne level, the UV ink may not properly adhere, leading to poor print quality, peeling, or ink lifting.
- Testing with a dyne pen:
- To check a substrate’s dyne level, a dyne pen is used to assess the surface energy, allowing you to determine if a primer or surface treatment is needed.
- Surface treatments to increase dyne levels:
- Methods like corona treatment, plasma treatment, or applying a dedicated adhesion promoter (primer) can be used to raise the dyne level of a low-surface-energy substrate, enabling better ink adhesion.
UV inkjet adhesion refers to the ability of UV-curable ink to firmly stick to a substrate (surface) when printed using an inkjet printer, where the ink is cured instantly by exposure to ultraviolet light, essentially creating a strong bond between the ink and the material it’s printed on; this bonding process is crucial for ensuring the printed image is durable and doesn’t easily peel off.
- UV ink properties:
- Unlike traditional inks, UV ink is designed to rapidly cure upon exposure to UV light, allowing for immediate adhesion to the substrate.
- Surface preparation:
- To achieve optimal adhesion, sometimes a primer or adhesion promoter is applied to the substrate before printing, especially on materials with low surface energy where the ink might not readily bond.
- Factors affecting adhesion:
- The quality of the UV ink, the surface characteristics of the substrate, the curing process, and the application of a primer can all influence the strength of the bond.
- Surface energy is the amount of energy stored at the surface of a material, essentially representing the disruption of intermolecular bonds that occurs when a new surface is created; it can be thought of as the “work” required to create a unit area of a new surface, and is often used to describe how well a material will adhere to other substances based on its molecular attraction at the surface.
Key points about surface energy:
- Definition:
- It’s the excess energy present at the surface of a material compared to its bulk, signifying the force of attraction between molecules at the surface.
- Measurement:
- Surface energy is usually measured in units of energy per unit area (like Joules per square meter).
- Application:
- Understanding surface energy is crucial in fields like adhesion, wetting, and material science, as it determines how well liquids will spread on a surface or how easily two materials can bond together.
Wettability
UV inkjet wettability is the ability of UV inkjet ink to spread out on a surface. It’s an important factor in the quality of printed images.
Factors that affect wettability
- Surface tension: The ability of a liquid to wet a solid surface. Lower surface tension means the ink can wet more surfaces.
- Contact angle: The angle at which the ink droplet meets the surfacestrong A smaller contact angle is better.
- Surface properties: The properties of the surface the ink is applied to, such as its chemistry and roughness
- Drop volume: The volume of the ink droplet
- Printing strategy: How the ink is applied to the surface
How wettability is important
- Adhesion: Wettability affects how well the ink sticks to the surface
- Streaks: Good wettability helps prevent streaks in the printed image
- Resistance to fading: Wettability helps prevent the ink from fading when exposed to moisture
How to improve wettability
- Adjust ink components
- The amount of monomers, oligomers, photoinitiators, pigments, and additives in the ink can be adjusted to improve wettability
Use UV irradiation
- UV irradiation can make surfaces more hydrophilic, which can improve wettability
- Use flame pre-treatment
- Flame pre-treatment can increase the surface energy of a substrate, which can improve wettability
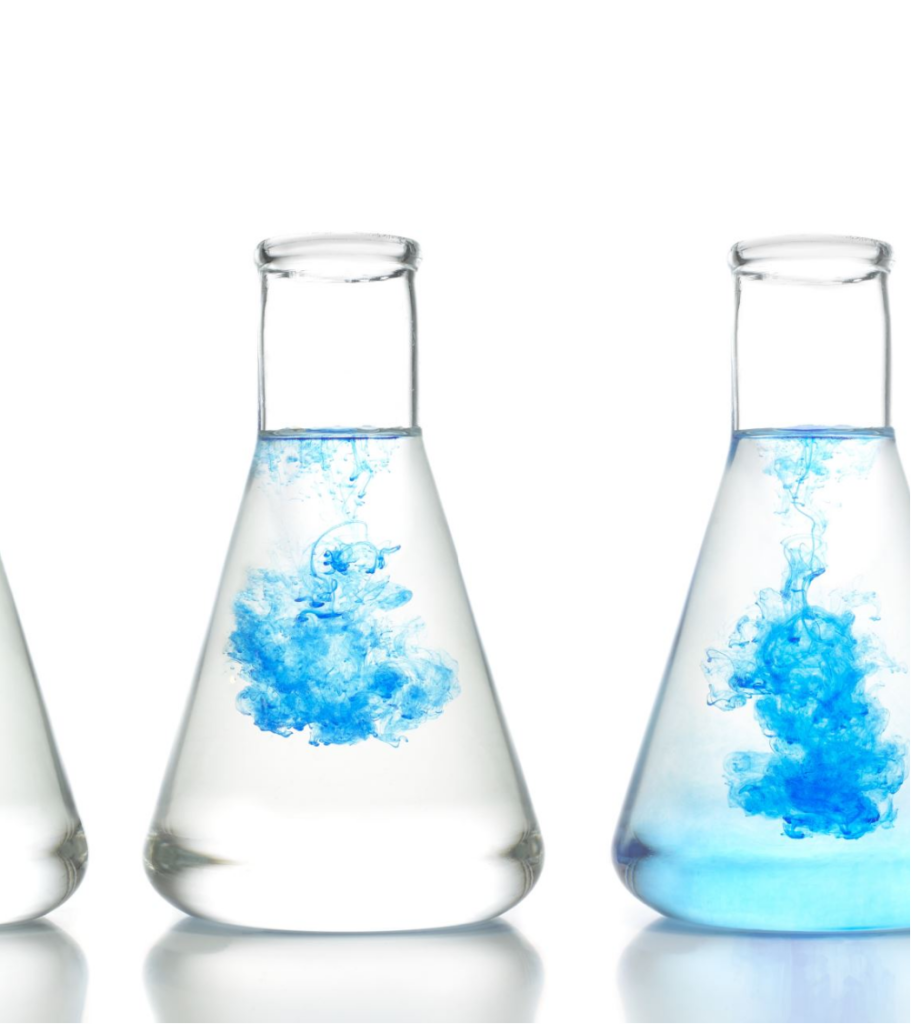
Dwell Time
“UV inkjet dwell time” refers to the amount of time an ink droplet from a UV inkjet printer spends exposed to ultraviolet light after being deposited on a substrate, essentially the time it takes for the UV light to fully cure the ink, transforming it from a liquid to a solid state; this is a very short duration due to the rapid curing nature of UV inks.
Key points about UV inkjet dwell time:
- Fast curing:
- Because of the quick reaction between UV light and the photoinitiators in the ink, the dwell time is usually measured in milliseconds.
- Impact on print quality:
- Proper dwell time is crucial for achieving optimal print quality, as too little time can lead to under-cured ink, while too much can result in potential distortion or damage to the substrate.
- Factors affecting dwell time:
- Factors like the intensity of the UV light, the ink formulation, and the speed of the print head can influence the necessary dwell time.
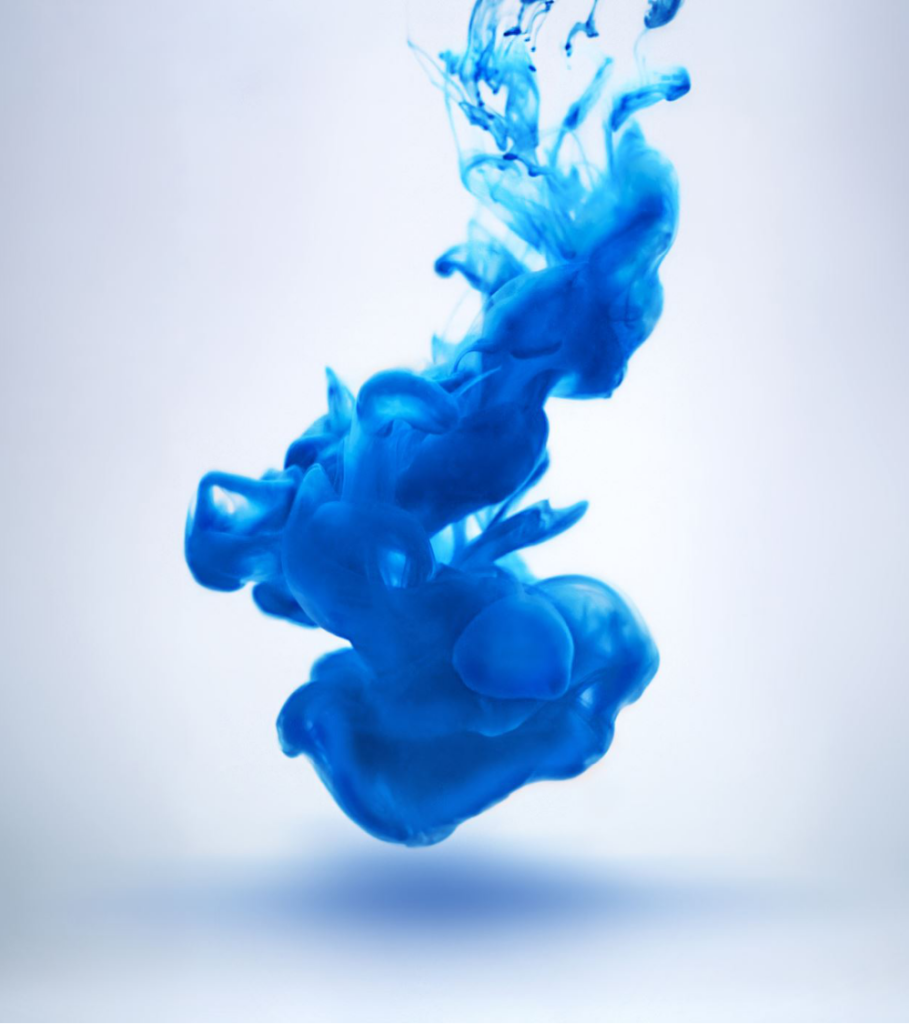